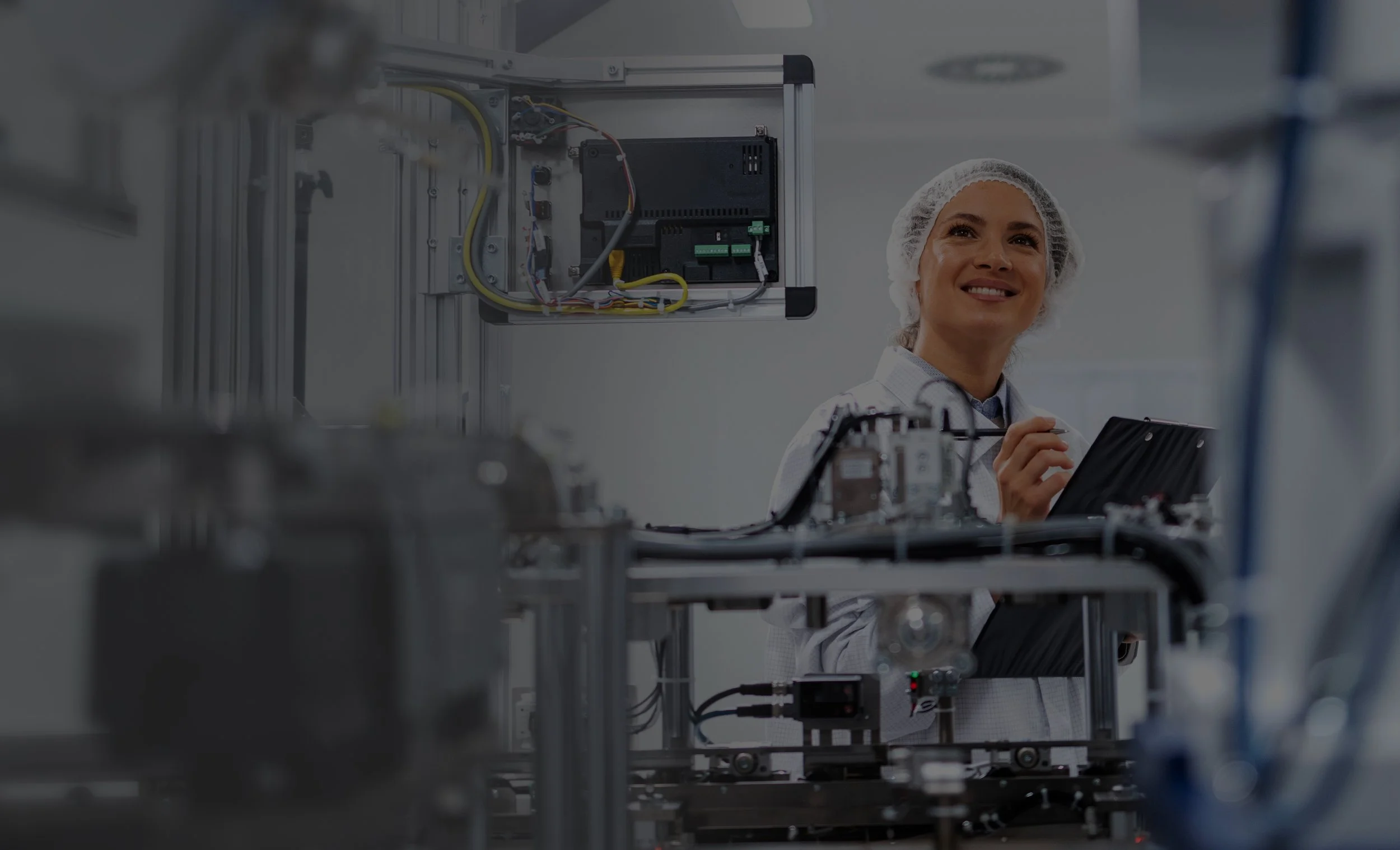
An AI platform that helps manufacturing companies
earn more by reducing losses at every stage of the process
Normalic identifies and eliminates production bottlenecks - from underutilization to regulatory violations.
What could possibly go wrong?
Absolutely everything.
Unless you are able to truly understand what happens, when it happens and why it happens in your production.
Data and dashboards are of little help if they are not actionable – you may still be losing money without even noticing it.
Our AI models engage only when it counts, delivering in-time insights — so you don’t overreact when you don’t have to.
Lack of in-time visibility
creates
inefficiency
Poor data quality
leads to
bad decisions
Siloed decision-making
slows
reaction time
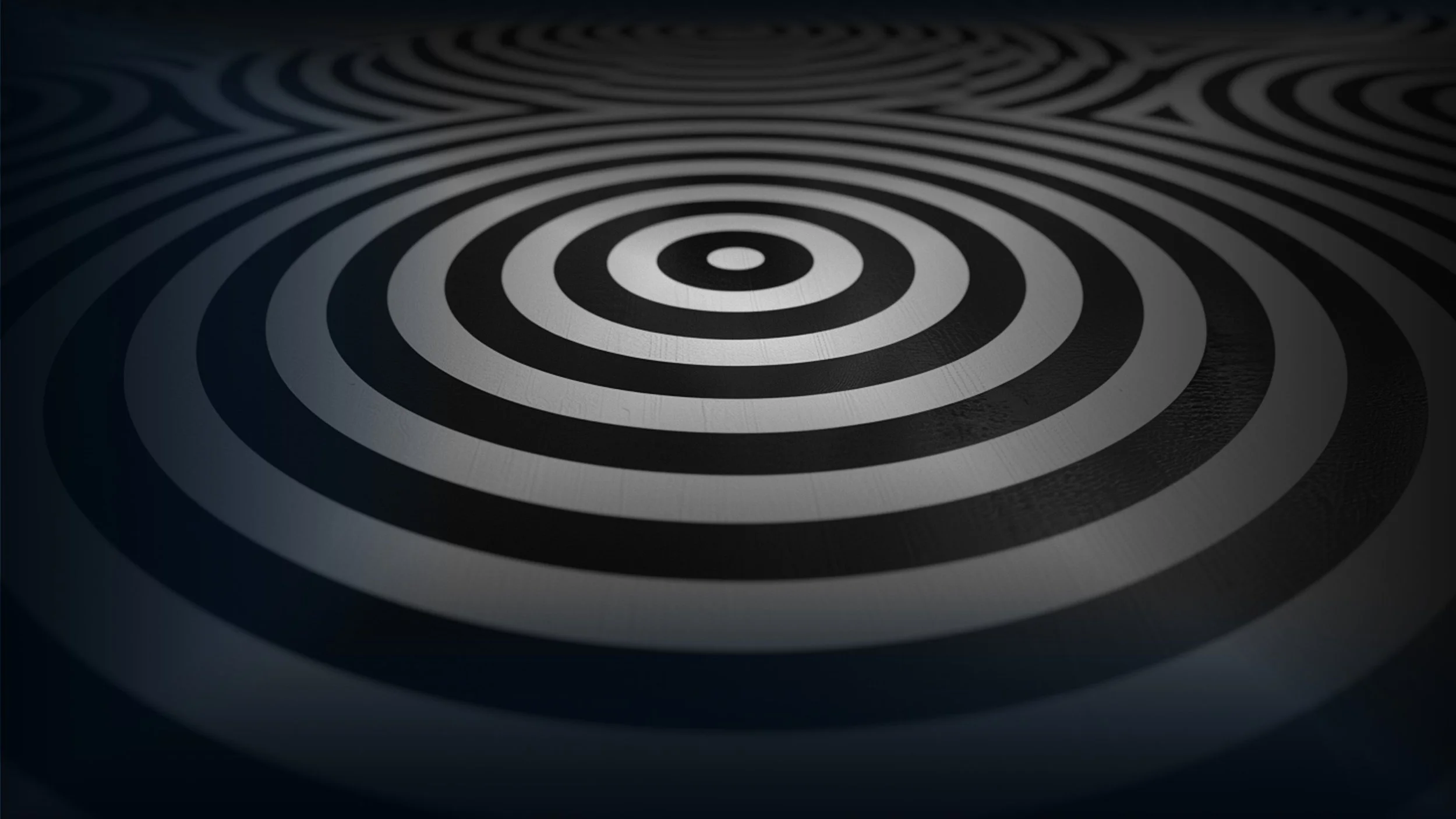
Normalic eliminates blind-spots
Every production company has them.
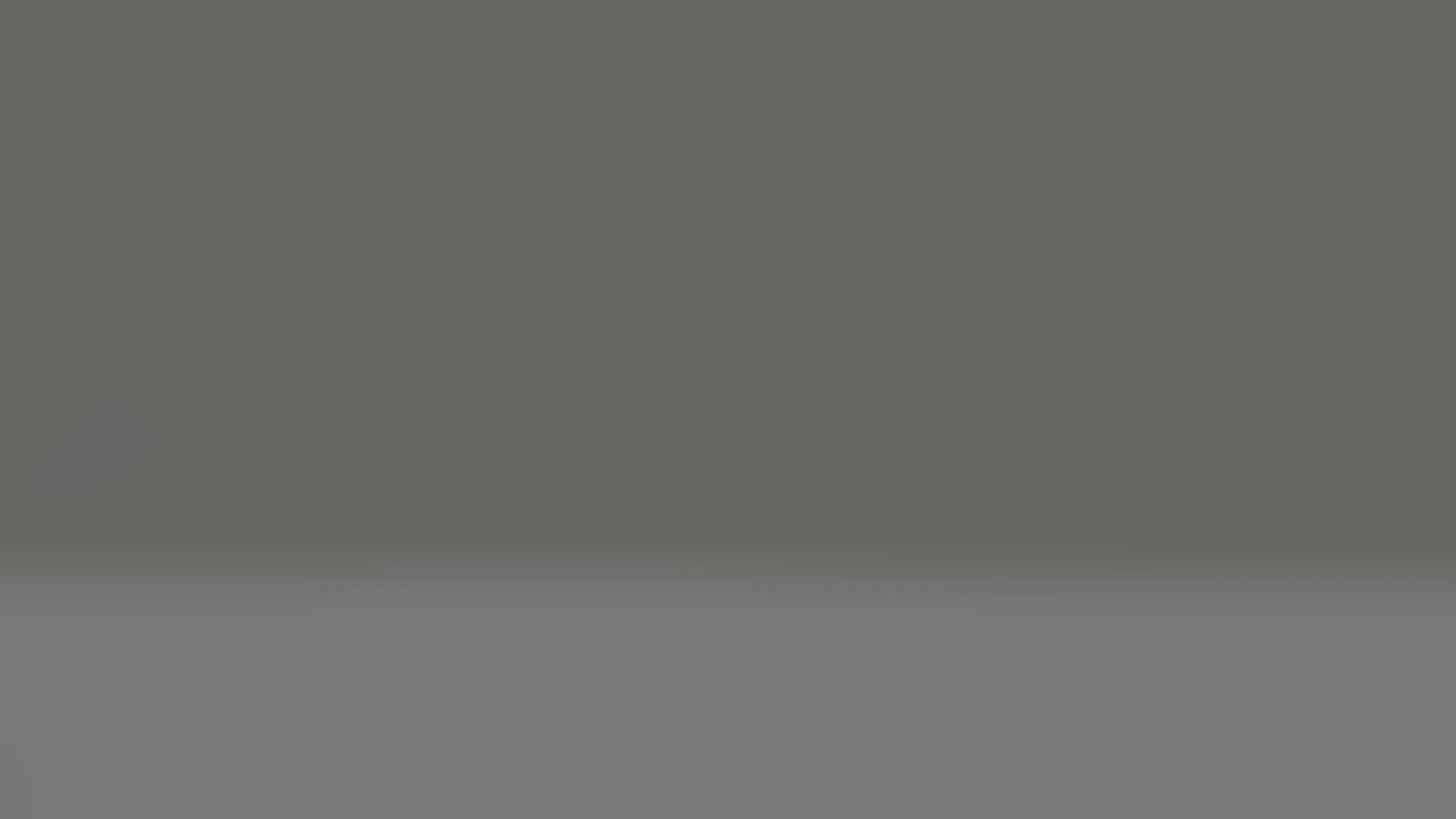
AI is the new normal
Normalic is a next-gen AI tool that gives management a clear, high-level view of the shop floor
Using in-time information, not just historical data, Normalic provides actionable insights for immediate improvements
Normalic integrates with all systems and uses AI-driven analytics to suggest improvements – not just report issues
Finding the optimal flow
Normalic analyses your manufacturing process and determines the normative flow for each parameter.
Based on this it prescribes a normative process for the complete manufacturing process.
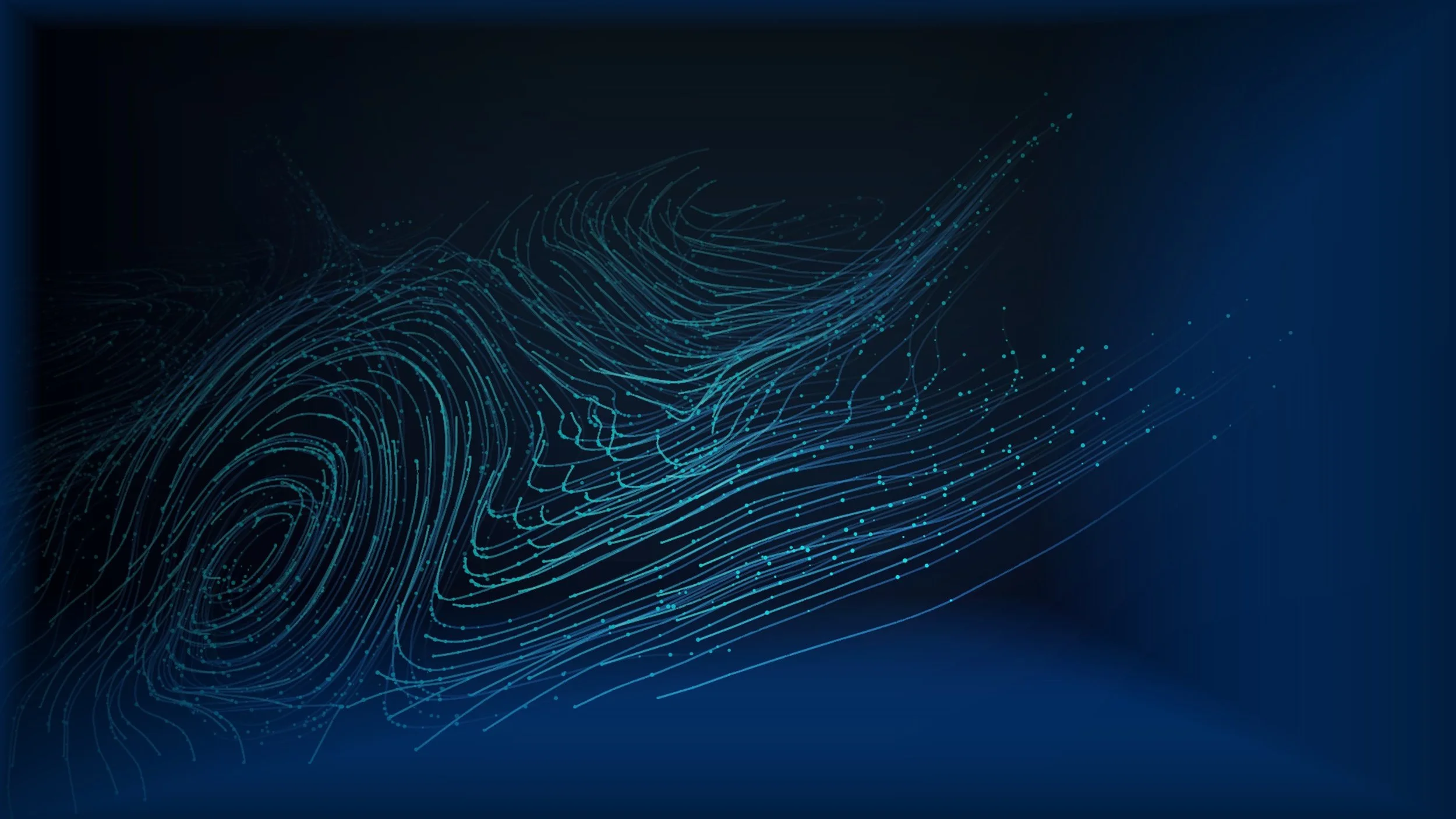
Normalic makes data work for you
Data collection from sensors, ERP integration, manual input
AI-driven analysis identifying inefficiencies, trends and anomalies
Dashboard providing simple, actionable insights
Automated notifications for the shop-floor and for decision makers
How does it work?
Each stage of our product is structured as a clear milestone. At every step, you have the opportunity to pause, reassess, and realign your needs and expectations.
We believe in flexibility, not lock-ins – you’re never tied in for longer than you choose.
1
Analysis and creation of production norms
Data acquisition and analysis from the whole process. The end result is a concise report of normative times and deviations, including cost of losses.
The report is a complete and valuable snapshot of your whole production, whether you continue with Normalic or not.
2
Creating automatic trigger system
A 4-month process with a dedicated Normalic consultant.
Assigns different trigger sensitivity to different roles. Considers the whole process from end-to-end.
Includes mentorship for key staff on what to observe, when to take action, and which improvements to consider.
3
AI Data Scientist is Online
Once the service is online it is continuously updated with new performance data.
Online service continuously evaluating and re-evaluating production efficiency, providing in-time notification to appropriate responsibility level.
4
Digital twin
After about 6 months of operation, a factory digital twin is available for virtual testing and optimisation.
Experiment with various changes to production and see their effects, before you apply them on the shop floor.